Insight into cost-effective and efficient solutions for the electrification of heavy vehicles
Doga Ceylan defended his PhD thesis with the distinction cum laude at the Department of Electrical Engineering on January 22nd.
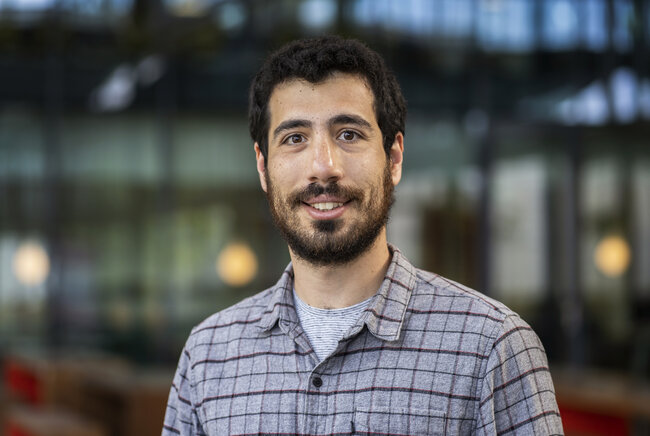
In this era of climate change awareness, fossil fuels' significant role in global warming is undeniable, mainly due to the greenhouse gas emissions resulting from their combustion. Worldwide legislation pursues each country to reach certain targets by boosting the electrification of different sectors, investing in new clean technologies, and providing affordable solutions towards increasing a circular economy. While considerable attention has been devoted to the design of on-road electric cars, particularly with diverse powertrain types, the application of electrical energy in off-road vehicles for heavy-duty purposes has been a relatively unexplored domain. This oversight is particularly pertinent in the agricultural sector, where off-road vehicles, such as tractors, play a significant role in transportation. The PhD research of Doga Ceylan not only contributes to the advancement of sustainable agricultural practices but also marks a significant stride towards achieving greener mobility solutions in heavy-duty off-road vehicles.
In the Netherlands, one of the leading countries in implementing clean and smart agricultural technologies, the electrification of the agricultural sector emerges as a critical step towards sustainability. However, this transition poses unique challenges, particularly in heavy-duty off-road vehicles. These challenges stem from the high load torque experienced by vehicles like tractors, a parameter highly dependent on soil conditions.
Cost-effective and robust solution
To address these challenges, Ceylan proposes an innovative solution: the Variable Flux Reluctance Machine (VFRM). Traditional permanent-magnet (PM) machines, while effective, present issues in terms of recyclability, increased costs, and reduced performance at higher temperatures due to demagnetization risks. The VFRM, being PM-free, offers a cost-effective and robust alternative for high-torque electrical drives. The unique aspect of the VFRM lies in its utilization of a direct current (dc) field to enhance torque density, in contrast to conventional permanent magnets. This not only reduces costs but also improves recyclability, dismantling, and overall durability. However, achieving high-torque operation with the VFRM requires a meticulous approach, involving a high level of current excitation that compels the laminated iron material in its rotor and stator to operate under local magnetic saturation. As a result, nonlinear electromagnetic modeling becomes indispensable in the design and analysis of the VFRM.
Innovative frameworks for electromagnetic precision
This research introduces several mathematical and experimental frameworks for iron-based electromagnetic devices, setting a new standard in modeling the precision of laminated soft-magnetic materials. The experimentally verified simulation models are used to create design and control methodologies for VFRM. An advanced field-oriented control algorithm is implemented for the constant-torque region based on optimal dc and ac-field excitations, while the maximum-torque-per-ampere method is applied for the flux-weakening operation. A design framework is facilitated by employing an evolutionary genetic algorithm. This approach aims to create cost-effective and robust electrical drives specifically tailored for a 3-ton electric tractor. The proposed optimization methodology encompasses both base and maximum speed operations, addressing the diverse needs of off-road farming and on-road transportation.
Performance breakthroughs in electrical design
The optimal design showcases remarkable capabilities. It can produce a maximum continuous torque of 200 Nm at a base speed of 1600 rpm. The efficiency stands at an impressive 90%, with a minimal torque ripple of 10%, a power factor of 0.7, and a torque density of 20 Nm/L during farming operations at the base speed. Moreover, the developed torque reaches 70 Nm at the maximum speed of 4266 rpm by implementing the proposed flux-weakening strategy, elevating efficiency up to 95% at high speeds.
In conclusion, the permanent-magnet-free design of the Variable Flux Reluctance Machine emerges as an economically viable and rapidly prototyped high-torque electrical drive solution for electric tractors.
Title of PhD thesis: Mathematical and Experimental Frameworks for Iron-based Electromagnetic Devices - Applied to Variable Flux Reluctance Machines for Heavy-duty Applications. Supervisors: Prof. Elena Lomonova and Dr. Konstantin Boynov.